Developer Flushes Traditional Bathroom Construction Method at NYC’s Prospect Plaza Housing
Residents of New York City’s new Prospect Plaza housing project in Brooklyn’s Oceanhill-Brownsville neighborhood likely do not realize there is something remarkable about the bathrooms in the complex.
Bathrooms are notoriously one of the most challenging aspects of constructing any multi-housing building – from apartments to hotels. “Historically, the number of trades and amount of coordination required in a bathroom exceeds pretty much any other area in a building,” explained Les Bluestone, Partner of Blue Sea Development Company, LLC, the project’s lead entity in a development partnership. “Anything that can reduce that bottleneck is helpful for completing a high-quality project on time and on budget.”
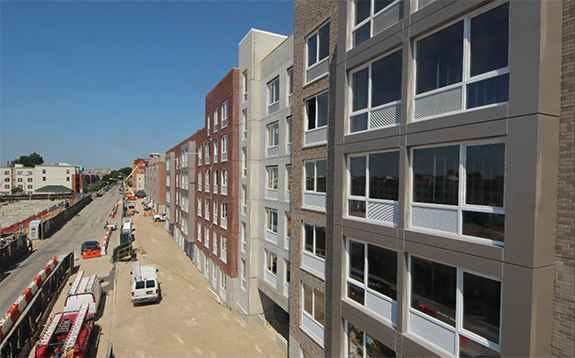 Prospect Plaza housing project under construction in Brooklyn’s Oceanhill-Brownsville neighborhood
Constructing a bathroom typically requires 10 or more construction trades – including electrical, plumbing and finishing work ranging from painting to mirror hanging – all working in an area of about 50 to 100 square feet. With so many workers coming and going in a confined area, there’s substantial risk of damage to previously completed work. As a result, bathroom rework accounts for about 60% of the punch-list in multi-housing projects. Such rework results in weeks of delay, which costs developers hundreds of thousands of dollars in financing fees and lost revenue.
In addition to the difficulties of constructing high quality bathrooms while keeping to a project schedule, Blue Sea Development faced another key challenge. To meet energy efficiency standards under several green building programs (Energy Star, National Green Building Standard and LEED) they needed to meet airtightness requirements between individual apartments and the exterior.
To streamline construction, while ensuring airtight, high quality bathrooms, the development team chose pre-fabricated modular bathrooms – New York City developers have been utilizing the advantages of modular and prefabricated solutions on a number of recent projects. Instead of being built on site piece-by-piece, the bathroom pods were constructed in a controlled factory setting. After being trucked to the project site, a crane lifted each pre-fab pod into place. Crews then were able to connect each modular bathroom quickly and easily to the building’s power, water supply and wastewater systems.
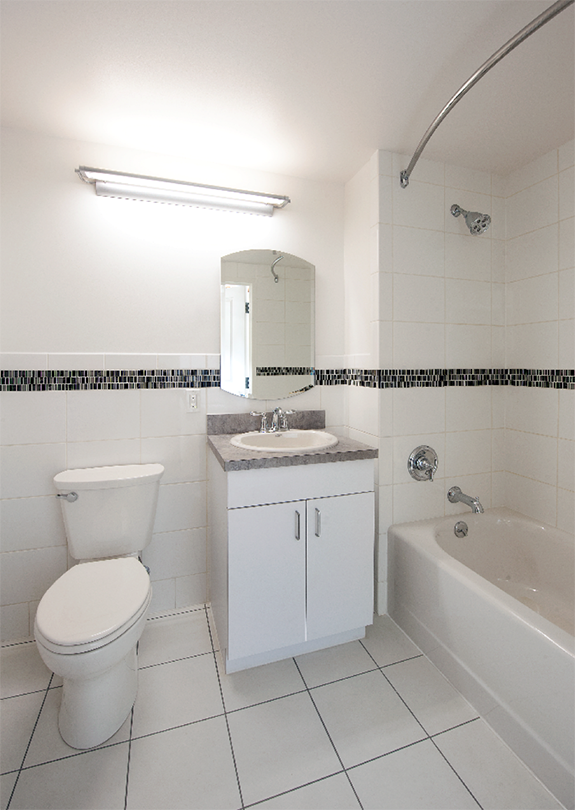 Interior view of pre-fabricated bathroom pods installed at Prospect Plaza
“Pre-fabricated bathroom pods eliminate the scheduling and construction hassles of having multiple sub-contractors working in a constrained space,” said Bill Seery, director of business development for Oldcastle® SurePods™ modular bathrooms. “You end up with a superior quality bathroom that’s completed faster so you can start renting or using your facility sooner.”
Commenting on the completed project, Bluestone added, “The bathrooms passed the airtightness requirement better than anything that could have been field constructed.”
Bluestone also noted that given the tight market for skilled construction labor and the fact Blue Sea was using precast concrete panels and floors that required a crane on site, the bathroom pods were “a good match for the project.”
Beyond facilitating construction for developers, Oldcastle® SurePods™ provide quality bathrooms for building tenants. “People are generally impressed when they see the quality of the Prospect Plaza bathrooms,” said Bluestone.
“We can build bathrooms to virtually any level of finish – from public housing to luxury hotels,” noted Seery. “Oldcastle® SurePods™ have been used in a full range of settings, from affordable housing to some of the country’s finest 5-star hotels. We are also a pre-approved supplier for top hotel brands including Marriott International and Hilton Worldwide.”
Blue Sea Development – recognized as one of the most innovative and creative developers of social housing – is building the multi-phase Prospect Plaza project on behalf of the New York City Housing Authority (NYCHA) and NYC Housing Preservation & Development (HPD). Prospect Plaza is transforming 4.5 acres in Brooklyn’s Oceanhill-Brownsville neighborhoods into 394 housing units, including 80 units of NYCHA public housing and 310 affordable housing apartments, retail space, a community center and a public park.
Watch a time-lapse video of the Oldcastle® SurePods™ installation in Prospect Plaza: https://oldcastlemodular.com/surepods-builds-multi-family-project-nyc/.
Summary
Project: Prospect Plaza
Building Type: Hope VI Public and Low Income Tax Credit housing
Developer: Oceanhill, LLC (Huntington, New York)
General Contractor: Blue Sea Construction (Huntington, New York)
Architect: Dattner Architects (New York City)
Project Status: Completed 2016
|